In recognition of Georgia Tech’s SDG Action and Awareness Week (March 6-10, 2023), the Ray C. Anderson Center for Sustainable Business (Center) is pleased to share an interview with sustainable business leader Bo Quick. Bo graduated from Georgia Tech in 1993 with a Bachelor of Industrial Engineering. He started his career as a consultant in environmental engineering and now serves as vice president of corporate sustainability and strategy at Southwire Company, a leading manufacturer of wire and cable used in the transmission and distribution of electricity. Southwire is one of the founding members of the Drawdown Georgia Business Compact – the Center’s initiative that leverages the collective impact of the Georgia business community to achieve net zero carbon emissions in the state through a just, prosperous, and sustainable transition. On March 3, 2023, Allison Bridges, the Compact’s program manager, sat down with Bo to learn about his background and Southwire’s commitment to sustainability.
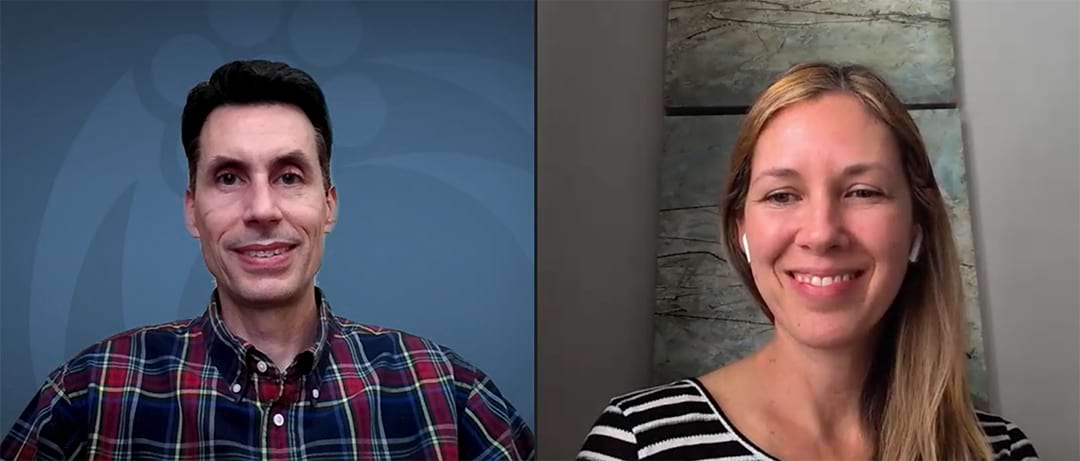
Allison Bridges: Thank you for taking the time to speak with me. I’m eager to hear about your work at Southwire, but would you first talk a bit about your early life?
Bo Quick: My dad was in the Army, so my family moved around a good bit. We lived in Germany, Kansas, and Alabama. Then, in the 1980s, we settled in the Atlanta area. Growing up, I played a lot of sports. When I was in junior high, Georgia Tech was very successful in basketball, so that got my attention. I ended up enrolling at Tech after I graduated from high school.
AB: What did you study at Georgia Tech?
BQ: I started out in management but switched to industrial engineering.
AB: Was there anything else you participated in at Georgia Tech?
BQ: I was in a fraternity. I worked on campus for the Georgia Tech Research Institute (GTRI). I played intramural sports: volleyball, basketball, softball, football…pretty much everything they offered!
AB: When did you get interested in sustainability?
BQ: The husband of the lady I worked for at GTRI moonlighted for an environmental engineering firm. He talked to me about his work, and it sounded interesting. He introduced me to an opportunity with Conversion Technology, and that’s where I started working. I was in the firm for a number of years. As for “sustainability” – that term didn’t start showing up until the early 2000s. I came on board at Southwire in 2007, and in 2008, the company rolled out its formal philosophy of sustainability with five tenets. The environmental group naturally took a lot of that responsibility to work towards the goals the company had set.
AB: What prompted you to make the switch from an environmental consulting firm to Southwire?
BQ: Over the course of the 12 years that I was in consulting, I did project work for over 200 companies. It’s kind of like dating, right? You meet the companies, go to the facilities, see what they do, and get a taste of their culture. In that process, I came across a few companies that made me think, “If I ever had the opportunity, I wouldn’t mind working for them.” Southwire was one of a handful of companies that I would even consider. One of the Southwire folks, who is a colleague now, reached out to me and said, “Hey, we’ve got an opportunity. Are you interested?” And I said, “Absolutely.” That was how I transitioned from consulting to being in the industrial and manufacturing sector.
AB: Were you working on a lot of projects in the industrial and manufacturing sector before you joined Southwire?
BQ: Definitely. My specialty is in air quality permitting and compliance. For about five years before 2007, Southwire was one of my key clients.
AB: How would you describe Southwire to someone who is unfamiliar with it?
BQ: Our core business is electrical wire and cable for homes and businesses. If you look up and see utility wires, that’s our work as well. We also make wires for appliances, automobiles – anything that transmits power. Our secondary business, which is a bit newer for the company, is providing tools to help contractors install our products. And now, we are going into services: looking at how we can help companies install cables, and how to help extend the life of cable. The latter aligns with sustainability. Rather than making new cables, we are finding ways to take something that is in service today and extend its life another 25 to 30 years.
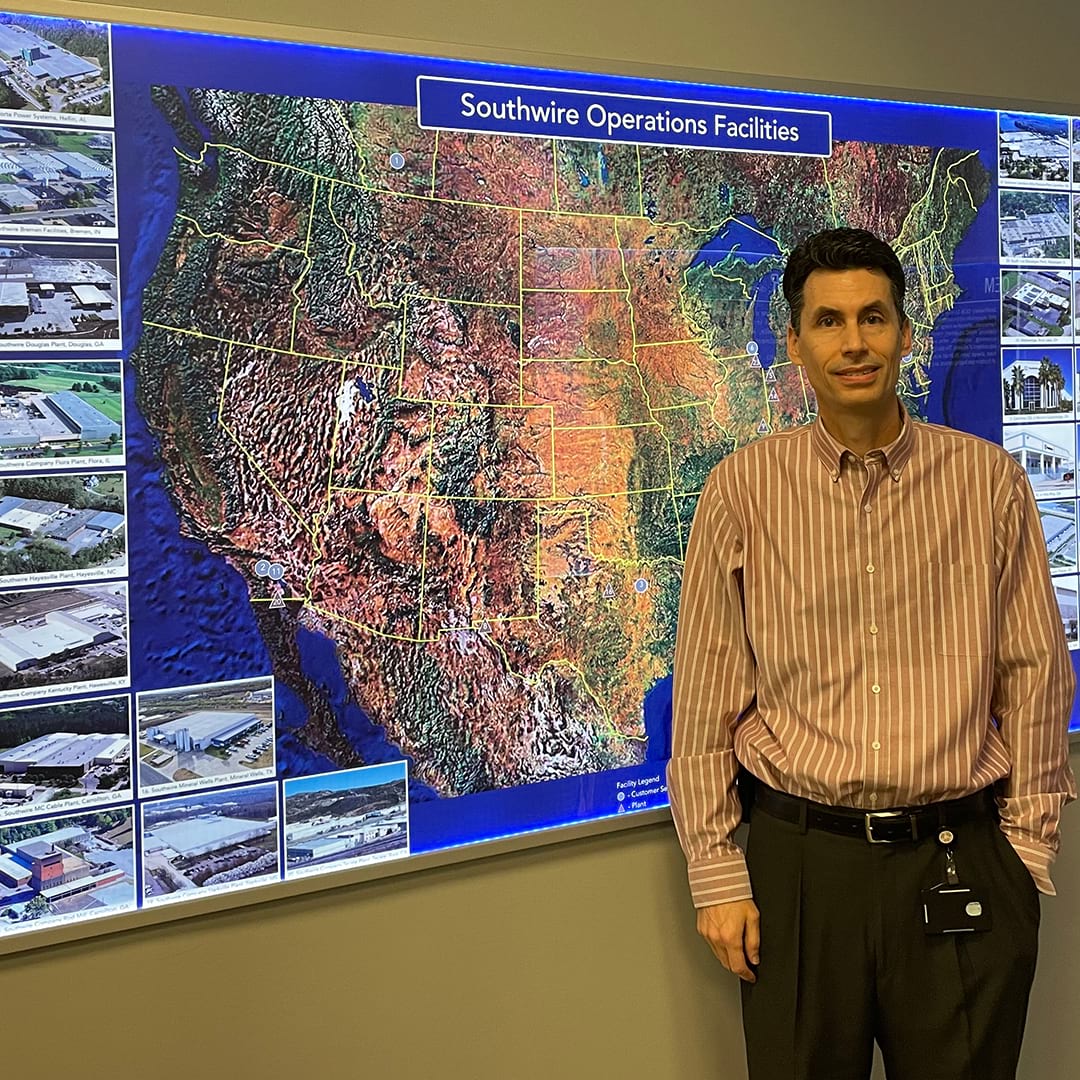
AB: Earlier you mentioned Southwire’s five tenets of sustainability. What are they?
BQ: “Growing Green” is about the environment, “Living Well” is employee experience, “Giving Back” is community involvement, and “Doing Right” is ethics and compliance. The final tenet, “Building Worth,” is our recognition that we are tied very much to our customers, employees, owners, suppliers, and communities. Our success is tied to the success of all those other stakeholders.
AB: You are currently vice president of corporate sustainability strategy. What does that role entail?
BQ: I’m on the corporate sustainability team that guides and implements corporate strategy. We report to our chief sustainability officer. We support him and bring him ideas. He has ideas that we try to implement. Our team is also tasked with engaging with different organizations such as the Drawdown Georgia Business Compact and companies that we meet through the Compact.
AB: I looked through Southwire’s sustainability report and saw a big focus on net-zero goals. They look pretty aggressive!
BQ: Yes, Southwire announced in the summer of 2020 that its goal is to be carbon neutral by 2025, and we’re on pace to do that. We’ve installed some solar applications, and we’re working hard on energy efficiency projects. In the short term, we will have to utilize RECs [renewable energy certificates] and carbon offsets. We’re pushing hard, but we want to be a leader.
AB: What are some of the challenges you face in reducing carbon emissions?
BQ: Southwire deals with metals. Aluminum and copper are the two main components of wire cable. We have to melt metal, and the best way to do that now is with natural gas. While we need to use carbon offsets in the short term, we are not letting the current technology limitations hamper our ambitions. We still want to go forward. How can we change the technology? How can we use a different fuel? Just because you can’t do something today, doesn’t mean that shouldn’t be the ambition.
AB: What about Southwire’s commitment to equity and community impact?
BQ: My team interacts with our DE&I and Giving Back teams. One of the things that shows Southwire’s long-term focus on sustainability would be our 12 for Life program, now in its sixteenth year. The company has a requirement that to work at our plant, you need a high school diploma or the equivalent. Southwire recognized that our city and county had a lot of kids who weren't graduating. We asked ourselves, “What can we do to boost the graduation rate?” In this 12 for Life program, we have a facility that is designed for students. Students who are identified as being at risk are invited to work half a day at the facility. They get paid and learn general job skills, like showing up on time and working with a team. The students are paired with mentors who help them acquire life skills as well. If there is a job opening at Southwire, the participants in 12 for Life get an advantage, including a higher wage. We’ve graduated over 2,500 students over the last 15 years. We’re really proud of that.
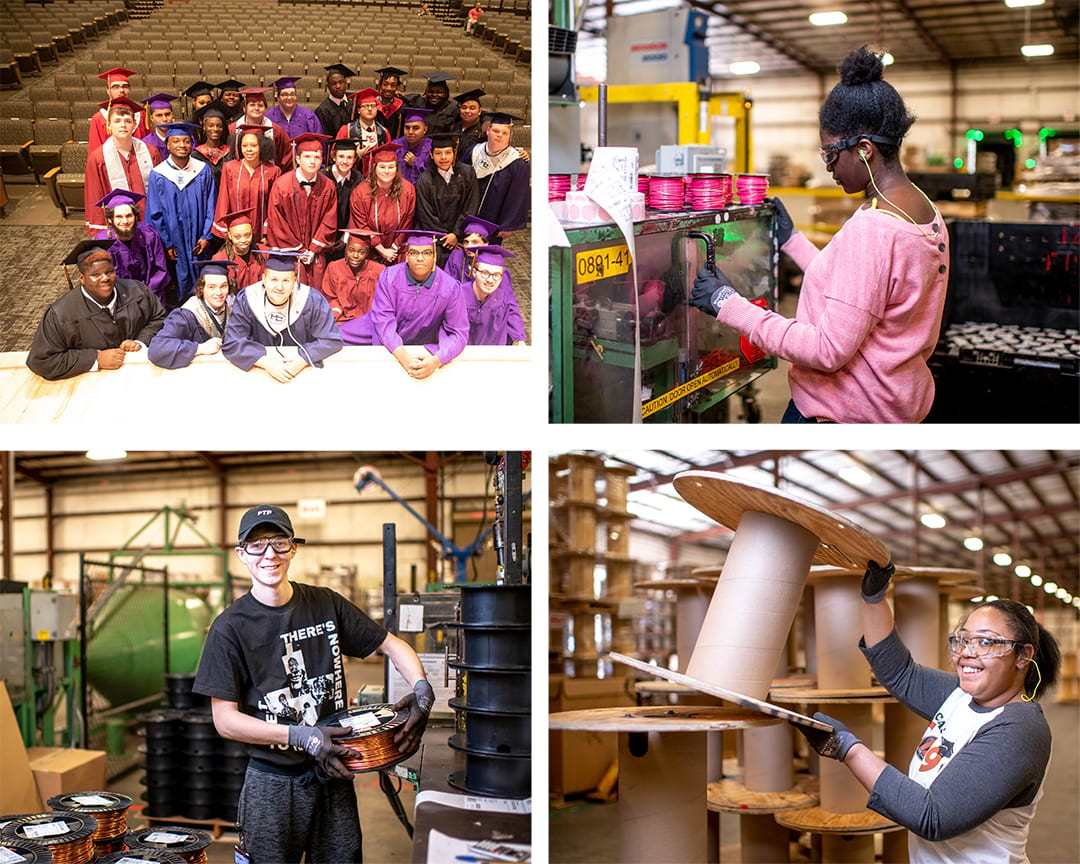
AB: Southwire has also been a client for our Center-led Sustainable Business Consulting Practicum, taught by Michael Oxman and Bob Lax. Can you talk about that experience?
BQ: We’re working with two teams right now [Spring 2023]. Last year, an MBA team helped us with a project based on our ambition to transition our fleet to electric vehicles. Southwire had a target date for the transition, but the team recommended that we back off from that type of thinking because the vehicles and infrastructure can’t yet meet our needs. They said we should start with a pilot process and have a measured pace to reach our goals. They did their research, and now Southwire can make an informed decision. That was very helpful for us. We can still keep our ambition but not set ourselves up for failure by aiming too high too soon.
AB: I know Southwire has partnered with The Ray, a movement to create net-zero highways, starting with a stretch of I-85 that serves as a learning lab. How are you engaging there?
BQ: We have a great relationship with The Ray on multiple fronts for about four years. Allie Kelly [executive director of The Ray] presented at a conference four years ago, and some of the things she said struck a chord with us. We decided that we needed to learn more about what The Ray is working on and see where there is overlap. For instance, one of things The Ray is focused on is how to use the highway right-of-way for high-voltage energy transmission. Well, that’s what we do. We make those cables. Because we have that technical expertise, we are helping them build their case as they talk to DOTs and others on how this can be successful.
AB: Because I myself am still relatively new to the Drawdown Georgia Business Compact (Compact), I’d love to hear your thoughts on how membership has been benefiting Southwire.
BQ: Building connections has been the biggest benefit for us. There are some companies that have similar ambitions that we have benchmarked with. Also, Southwire is talking to Goodr about solving our composting challenge. We have composted in the past, but the available outlets for composting have been limited in our corporate office area.
AB: What advice would you give students interested in working in sustainability?
BQ: First, be open to opportunities. Just because a company isn’t a name brand doesn’t mean it’s not a good place to work. Second, business leadership speaks a common language about money, finance, and return on investment. Even if leadership doesn’t understand sustainability, they understand the financial side. You need to be able to sell the value of sustainability. Can it enhance employee retention and talent attraction? Can it help build the company’s relationship with a regulatory agency or community stakeholder?
AB: If you had a job opening, what skills would you look for in an applicant?
BQ: The applicant needs to have technical skills. Also, the ability to communicate – up and down the line and across the organization laterally – is a big piece. A lot of the things we are working on now relate to building our internal and external messaging and branding. Employee engagement is also important. A lot of the things we do in sustainability don’t necessarily resonate with the operator on the floor. We need to educate our employees on what sustainability is and give them the opportunity to share their ideas.
AB: Finally, what are your favorite things to do in your spare time?
BQ: My wife and I like to read books and watch movies. Right now, we’re watching the old Mission Impossible TV series. It’s funny to see what they thought spycraft was back in the ’60s. I’m active in my church. I have two children in college. One is graduating this year, and one is on track to graduate next year. So, we value time spent together as a family.
AB: Thank you so much for speaking with me today. I’ll see you at our next Compact event!
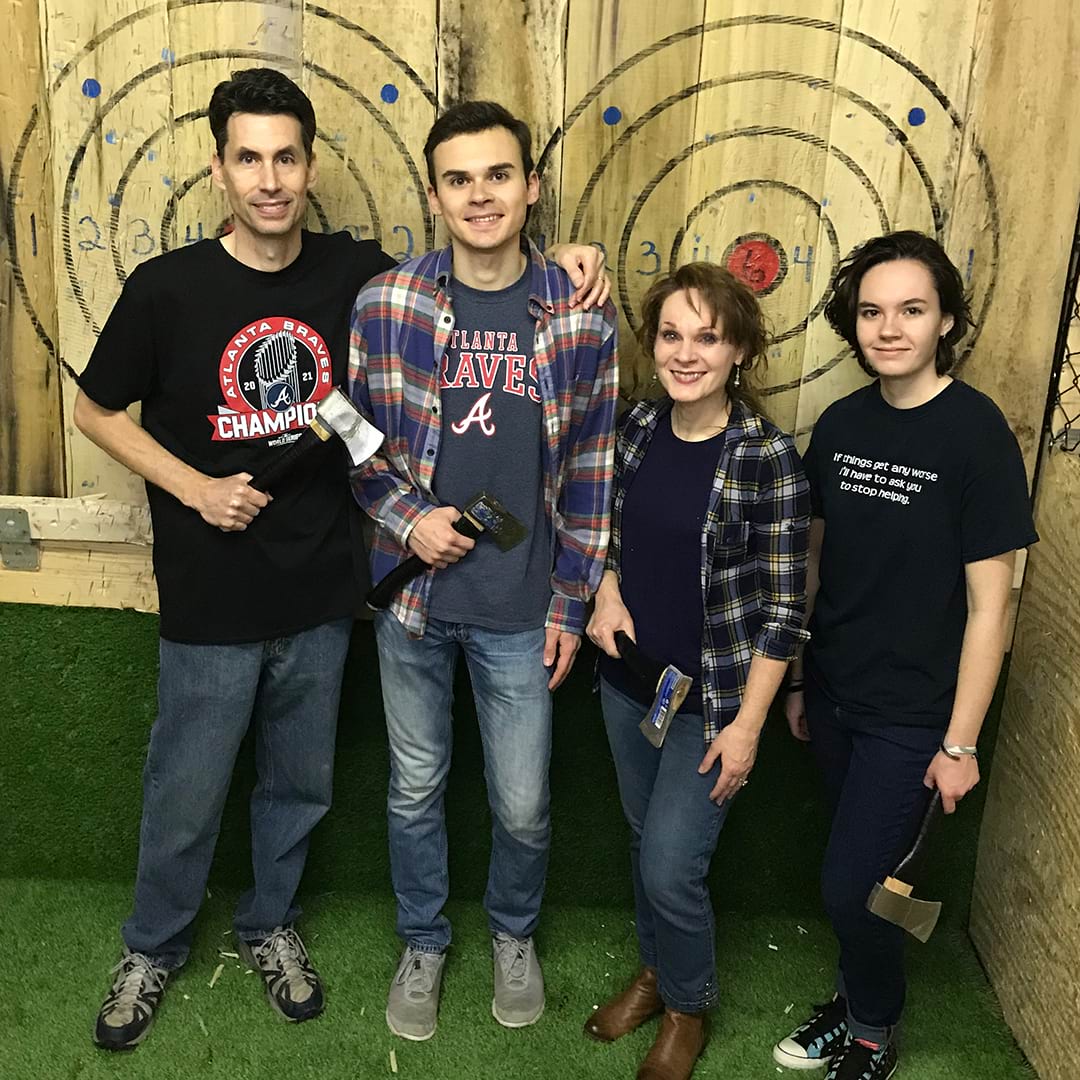
As told to Jennifer Holley Lux